Our planet has finite resources, and it is crucial that we rethink the way we live and interact with our environment to ensure a prosperous future for the generations to come. This requires a reconsideration of how we produce and consume goods as well as our personal habits.
The concept of circular economy involves collecting and reusing products and materials as much as possible before recycling or disposing them, and thus keeping resources in the economic loop for as long as possible [1].
However, incorporating the concept of circular economy into product development adds an extra layer of complexity to an already multifaceted process. Developing a product requires that engineers and designers consider various factors such as aesthetics, function, cost, and user experience; design choices made during this process also influence the circular economy performance of products. One way to address this complexity is by breaking the product development process down into smaller, easier-to-manage problems and analysing the impact of each decision on the final product in terms of its sustainability and circularity performance. For example, while using glue to attach two components may be a quick and cost-effective fastening solution, it may hinder the product’s disassembly in the future and consequently the potential for material recovery.
UNLOCKING PRODUCT CIRCULARITY – DESIGN FOR CIRCULAR DISASSEMBLY
Within the EU-funded CircThread project, we have developed a new design method to tackle this complexity, enabling manufacturers to assess and improve their products from the perspective of achieving more circular products. The method, known as Design for Circular Disassembly or DfCD for short, helps answer critical questions such as:
- Q1 – How simple is it to disassemble my product when it reaches the end of its life?
- Q2 – How circular is my product?
- Q3 – What design changes can I make to maximize my product’s circular potential?
Let’s take a closer look at how the DfCD methodology works using the example of an electric kettle (Figure 1).
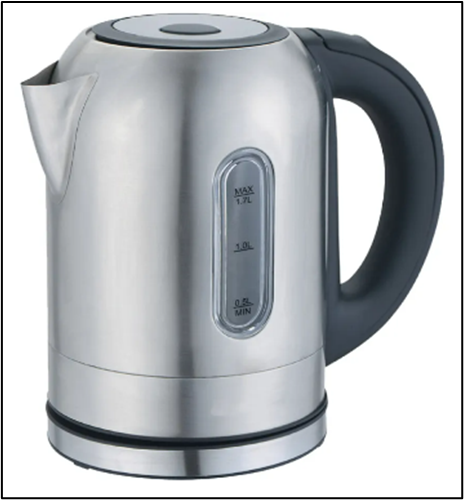
HOW SIMPLE IS TO DISASSEMBLY MY PRODUCT AT ITS END OF LIFE?
To answer the first question, we need to assess how easy is it to disassemble the electric kettle. This involves:
- Following the manufacturer’s recommended disassembly instructions (or trying to figure them out if they are not provided).
- Estimating how long it takes to complete the disassembly process (using a stopwatch or timer).
Overall, it took around 3 minutes and 30 seconds (or 210 seconds) to fully disassemble the electric kettle, involving 14 individual steps. It is important to notice that we used a kettle in perfect condition, without any damage or wear-and-tear. From now on, we will refer to this condition as the benchmark condition.
When products reach their end-of-life they are rarely in the benchmark condition. Therefore, it is essential to evaluate how the disassembly process might be affected by the product’s actual condition. In other words, it’s crucial to assess how easy (or hard) it would be to disassemble the product if it has been damaged or has wear-and-tear.
Suppose we have an electric kettle that is not perfect and has encountered some typical issues that can affect the disassembly process. Such issues are termed Disassembly Failures (DFs) in the DfCD method, and we will examine the following three examples (Figure 2) to illustrate this:
DF 1) The screws fixing the bottom part of the kettle are blunt or worn out.
DF 2) The cable may be broken during the disassembly process.
DF 3) Two parts of the kettle may be merged/fused due to a malfunction.
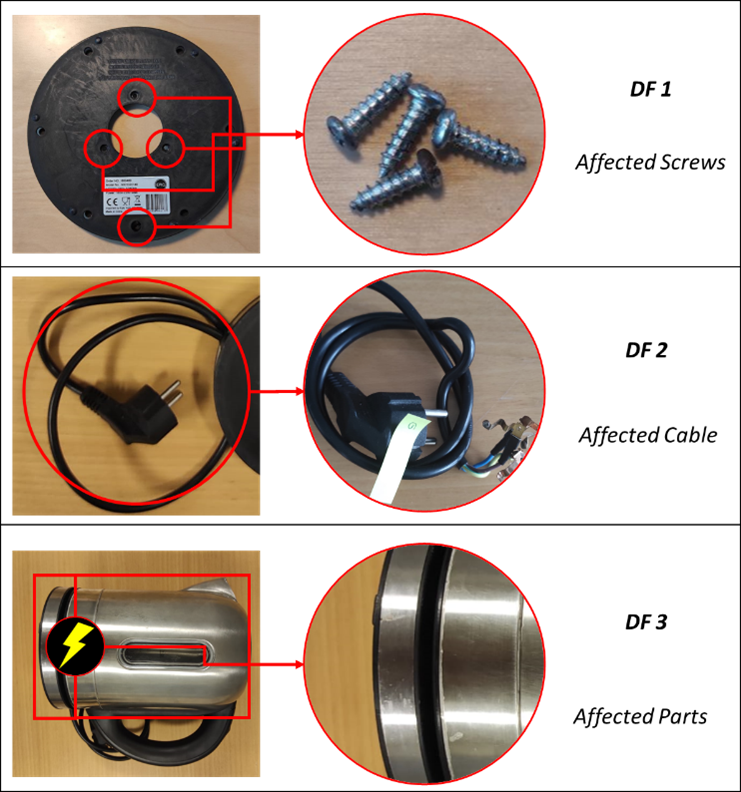
When faced with such scenarios, extra measures may be necessary to continue with the disassembly process. For instance, to tackle DF 1, we might need to drill out the screws, whereas for DF 2, we may have to dispose the entire cable. As for DF 3, the disassembly process could be excessively time-consuming, resulting in the disposal of the entire kettle. Thus, DFs can have a direct impact on the duration of disassembly operations, either increasing or decreasing it. We can estimate the increase or decrease in time required by analysing the (additional) actions that need to be performed. For instance, drilling out a screw would involve going to the drilling station, obtaining the drill and drill tips, returning to the disassembly desk, sitting down, and placing the drill on the screw. To help with this process, we can use a modified version of the well-known Maynard Operation Sequence Technique (MOST), called modified MOST [2].
How circular is my product?
Once we have identified DFs and estimated the time required to resolve them, we must evaluate the impact of the failures on the circularity performance of the product and its components. In other words, how will the DFs affect the ability to reuse or recycle components? Components that are free of issues can be directly reused without any modifications. However, if a component experiences a DF, we must consider how it can be repaired, recycled, or disposed.
Suppose we face DF 1, then we might have to dispose the screws by sending them to a landfill, as they are not useful after being drilled out. Similarly, in the case of DF 2, we may need to discard the cable, and for DF 3, we might need to dispose of the whole kettle at a recycling station. To sum up the information we have gathered thus far:
- we have the benchmark time required to disassemble the product in its benchmark (perfect) condition.
- we have the time required to solve disassembly failures (DFs).
- we have knowledge about the circularity of the product
“a perfect component can be reused, while one subjected to a DF can be either repaired, recycled, or disposed depending on the nature of the failure.”
We can combine all this information using some equations to calculate two important indicators: the Disassembly Effort Index (DEI) and the Circularity Index (CI). The DEI tells us how much effort is required to disassemble a product (a high effort translates to a high index value), while the CI indicates how circular the product is. A fully circular product would have a CI score of 1, while lower scores indicate lower levels of circularity performance. A fully linear product (i.e., where all materials are disposed at its end of life) would have a CI score of 0.
What design changes can I make to maximize its circular potential?
Analysing our example, we identified a total of 17 DFs that the electrical kettle may experience at the end of its life. These DFs represent various challenges that can arise during the disassembly process.
The figure below illustrates, on the x-axis, the difference between the time required to disassemble a product in benchmark condition and the time required to disassemble a product that has encountered each DF. On the y-axis, we can see the corresponding decrease in circularity performance due to each DF.
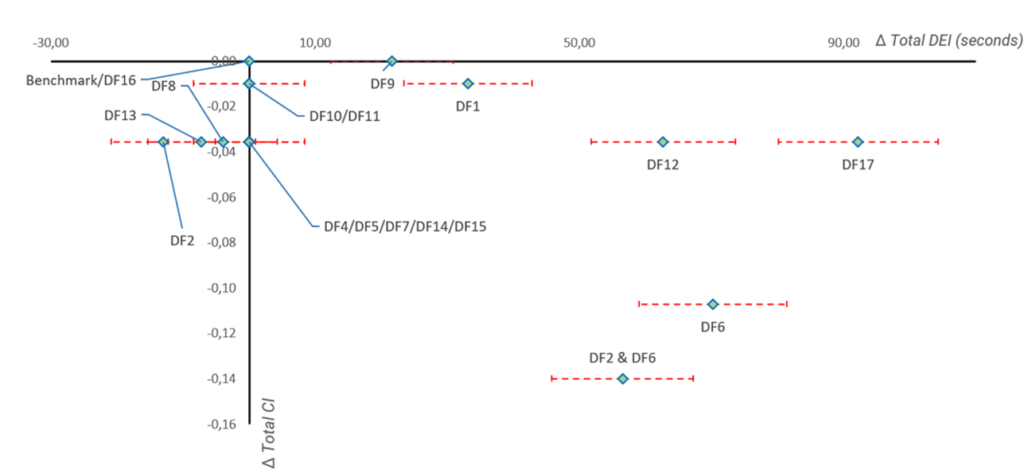
To achieve maximum circularity performance as well as efficiency in disassembling the electrical kettle at its end of life, we need to minimize the time required for disassembly and maximize the number of reusable components. To accomplish this, we should focus on avoiding DF 17, which would significantly increase the time and effort required to disassemble the kettle. By addressing the potential causes of this failure, we can improve the overall circularity performance of the product. DF 17 assumes that screws of the kettle body are rusted. Thus, to avoid the DF 17 it might be possible to:
- Change the screw material, for instance replace the original screws with stainless steel screws (Figure 4).
- Change the fastener type, for instance from screws to snap-fits (Figure 4).
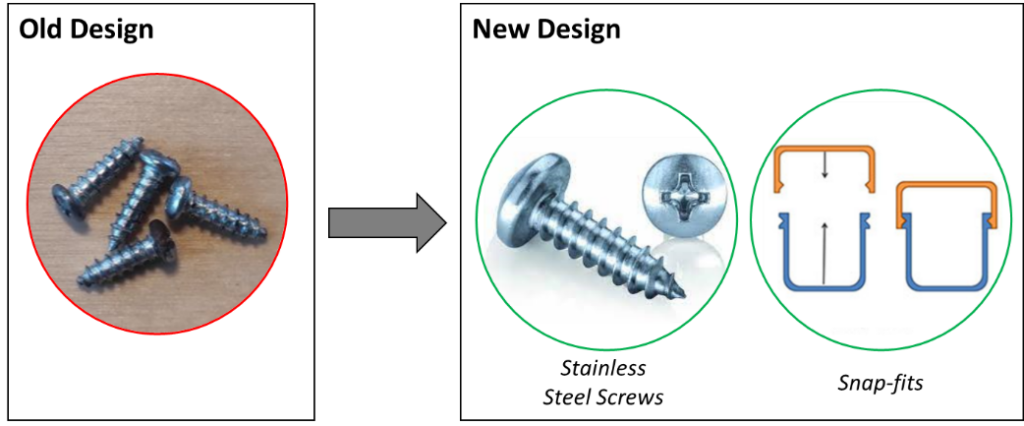
On the other hand, to increase kettle circularity, we should avoid DF 6. DF 6 states that the metallic parts of the thermostat, and its screws are bent. Thus, a potential design improvement could involve:
- Changing the thermostat system, for instance placing the metallic parts in a safer place.
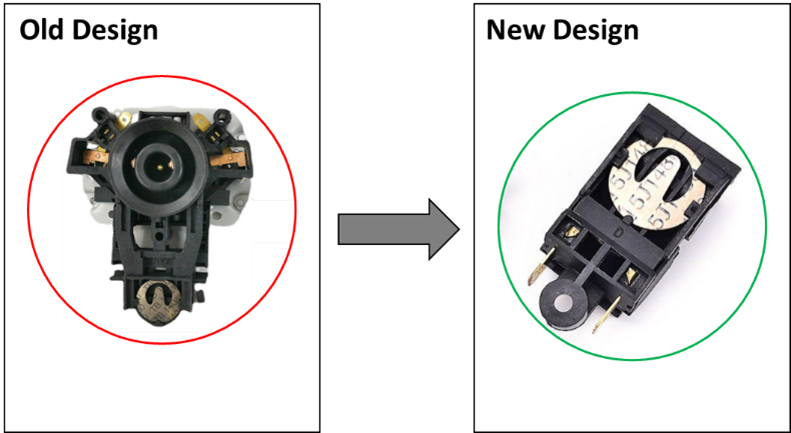
By conducting the same analysis for all 17 DFs, we can identify avenues for improving the original kettle design so that it is easier to disassemble and is more circular.
To sum up, the analysis performed allowed us to understand the shortcomings in terms of disassembly time and circularity of our product, as well as how a design improvement could benefit the product’s disassembly and circularity performances.
In addition, this analysis provides us with the opportunity to approach our design from a different perspective. The analysis reveals that without taking potential DFs into account, designers may have an incomplete understanding of their product.
This finding is illustrated with a practical example below.
In the figure below (Figure 6), we have collected all the actions required to perform the disassembly of the kettle. These actions have two DEI values, one is the benchmark value (i.e., perfect product), and the other is the value assuming that DF 1 is present.
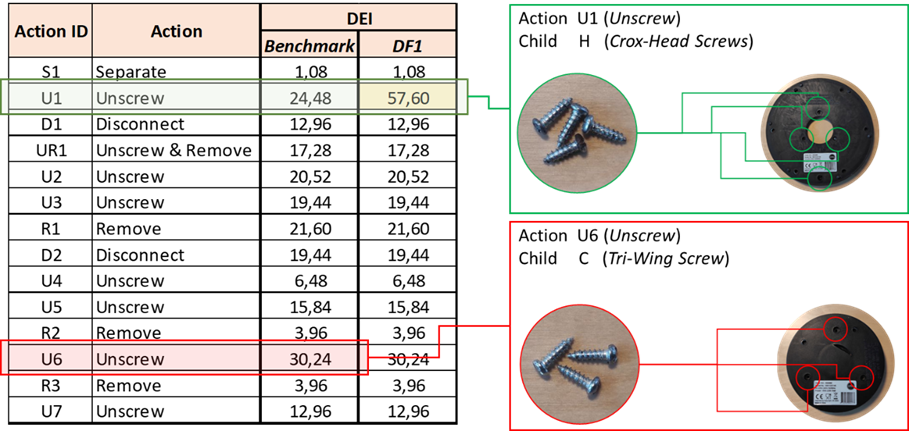
If we do not take DFs into account, we will incorrectly assume that the bottleneck of the disassembly process is the action U6, which is highlighted in red, and it should be improved by changing the fastener type, such as from screws to snap fits. However, if we consider the possibility of DFs, the most critical action becomes U1; improving U6 would only provide limited benefits. Therefore, the product’s design should be improved to avoid DF 1, and a new fastener type should be mandatory for action U1. This is an important insight and emphasizes the real-world value of the DfCD approach!
We have discussed how the DfCD can be applied to evaluate and enhance the circularity and disassembly capabilities of real products. For those who are interested, more detailed information can be found in our article published in the Journal of Cleaner Production [3].
The DfCD framework is an important step towards a completely new way of thinking, developing, creating, and using products in a more sustainable and circular manner. It is an exciting and ambitious idea and requires continued effort and collaboration from individuals, companies, and governments alike, to translate the obtained insights into practical gains. So, let’s continue to work towards a more sustainable and circular future, one product at a time! Don’t miss out on the latest updates and developments related to the EU-funded CircThread project. Follow us to stay up to date on further developments in the DfCD approach!
———————————————————————————————————————————————————————————————-
References
[1] MacArthur, F. E. (2013). Towards the Circular Economy Vol. 1: an economic and business rationale for an accelerated transition. Ellen McArthur.
[2] Formentini, Giovanni, and Devarajan Ramanujan. “Accounting For Product End-of-Life Status in Disassembly Time Estimation Using Modified Maynard Operation Sequences.” Procedia CIRP 116 (2023): 305-311. https://doi.org/10.1016/j.procir.2023.02.052 [3] Formentini, Giovanni, and Devarajan Ramanujan. “Design for circular disassembly: Evaluating the impacts of product end-of-life status on circularity through the parent-action-child model.” Journal of Cleaner Production 405 (2023): 137009. https://doi.org/10.1016/j.jclepro.2023.137009
Written by Giovanni Formentini (giof@mpe.au.dk) from Aarhus University